industrial internet of things (IIoT)
What is the industrial internet of things?
The industrial internet of things (IIoT) is the use of smart sensors and actuators to enhance manufacturing and industrial processes. Also known as the industrial internet or Industry 4.0, IIoT uses the power of smart machines and real-time analytics to take advantage of the data that "dumb machines" have produced in industrial settings for years. The driving philosophy behind IIoT is that smart machines are not only better than humans at capturing and analyzing data in real time, but they're also better at communicating important information that can be used to drive business decisions faster and more accurately.
Connected sensors and actuators enable companies to pick up on inefficiencies and problems sooner and save time and money, while supporting business intelligence efforts. In manufacturing, specifically, IIoT holds great potential for quality control, sustainable and green practices, supply chain traceability, and overall supply chain efficiency. In an industrial setting, IIoT is key to processes such as Predictive maintenance (PdM), enhanced field service, energy management and asset tracking.
How does IIoT work?
IIoT is a network of intelligent devices connected to form systems that monitor, collect, exchange and analyze data. Each industrial IoT ecosystem consists of:
- connected devices that can sense, communicate and store information about themselves;
- public and/or private data communications infrastructure;
- analytics and applications that generate business information from raw data;
- storage for the data that is generated by the IIoT devices; and
- people.
These edge devices and intelligent assets transmit information directly to the data communications infrastructure, where it's converted into actionable information on how a certain piece of machinery is operating. This information can be used for predictive maintenance, as well as to optimize business processes.
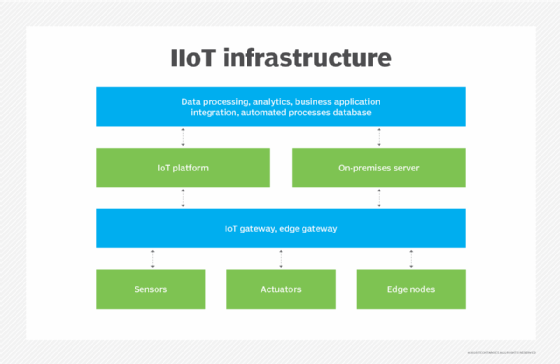
Which industries are using IIoT?
There are countless industries that make use of IIoT. One example is the automotive industry, which uses IIoT devices in the manufacturing process. The automotive industry extensively uses industrial robots, and IIoT can help proactively maintain these systems and spot potential problems before they can disrupt production.
The agriculture industry makes extensive use of IIoT devices, too. Industrial sensors collect data about soil nutrients, moisture and more, enabling farmers to produce an optimal crop.
The oil and gas industry also uses industrial IoT devices. Some oil companies maintain a fleet of autonomous aircraft that can use visual and thermal imaging to detect potential problems in pipelines. This information is combined with data from other types of sensors to ensure safe operations.
What are the benefits of IIoT?
One of the top touted benefits of IIoT devices used in the manufacturing industry is that they enable predictive maintenance. Organizations can use real-time data generated from IIoT systems to predict when a machine will need to be serviced. That way, the necessary maintenance can be performed before a failure occurs. This can be especially beneficial on a production line, where the failure of a machine might result in a work stoppage and huge costs. By proactively addressing maintenance issues, an organization can achieve better operational efficiency.
Another benefit is more efficient field service. IIoT technologies help field service technicians identify potential issues in customer equipment before they become major issues, enabling techs to fix the problems before they inconvenience customers. These technologies might also provide field service technicians with information about which parts they need to make a repair. That way, the technician has the necessary parts with them when making a service call.
Asset tracking is another IIoT perk. Suppliers, manufacturers and customers can use asset management systems to track the location, status and condition of products throughout the supply chain. The system sends instant alerts to stakeholders if the goods are damaged or at risk of being damaged, giving them the chance to take immediate or preventive action to remedy the situation.
IIoT also allows for enhanced customer satisfaction. When products are connected to the internet of things, the manufacturer can capture and analyze data about how customers use their products, enabling manufacturers and product designers to build more customer-centric product roadmaps.
IIoT also improves facility management. Manufacturing equipment is susceptible to wear and tear, which can be exacerbated by certain conditions in a factory. Sensors can monitor vibrations, temperature and other factors that might lead to suboptimal operating conditions.
Is IIoT secure?
Early on, manufacturers created IoT devices with little regard for security, resulting in a perception that IoT devices are inherently insecure. Given the similarities between IoT and IIoT devices, it's worth considering whether it's safe to use IIoT devices.
As with any other connected device, IIoT devices must be evaluated on a device-by-device basis. It's entirely possible that one manufacturer's device is secure while another isn't. Even so, security is a bigger priority among device manufacturers than ever before.
In 2014, several technology companies including AT&T, Cisco, General Electric, IBM and Intel came together to form the Industrial Internet Consortium (IIC). Although this group's primary objective is to accelerate the adoption of IIoT and related technologies, it's making security a priority, even going so far as to form a security working group. The IIC's other working groups include Technology, Liaison, Marketing, Industry and Digital Transformation.
What are the risks and challenges of IIoT?
The biggest risks associated with IIoT use pertain to security. It's relatively common for IIoT devices to continue using default passwords, even after they have been placed into production. Similarly, many IIoT devices transmit data as clear text. These conditions would make it relatively easy for an attacker to intercept the data coming from an IIoT device. Similarly, an attacker could take over an insecure IIoT device and use it as a platform for launching an attack against other network resources.
Security is a big challenge for those who are responsible for an organization's IIoT devices, but so, too, is device management. As an organization adopts more and more IIoT devices, it will become increasingly important to adopt an effective device management strategy. More specifically, organizations must be able to positively identify IIoT devices to prevent the use of rogue devices. Establishing a means of identifying each individual device is also crucial for tasks such as replacing a failed device or performing a device refresh.
Patch management presents another big challenge regarding IIoT devices. It's becoming increasingly common for device manufacturers to issue periodic firmware updates. Organizations must have an efficient means of checking devices to see if they have the latest firmware installed and deploying new firmware if necessary. Additionally, such a tool must adhere to the organization's established maintenance schedule so as to not disrupt operations.
What is the difference between IoT and IIoT?
Although IoT and IIoT have many technologies in common, including cloud platforms, sensors, connectivity, machine-to-machine communications and data analytics, they are used for different purposes.
IoT applications connect devices across multiple verticals, including agriculture, healthcare, enterprise, consumer and utilities, as well as government and cities. IoT devices include smart appliances, fitness bands and other applications that generally don't create emergency situations if something goes amiss.
IIoT applications, on the other hand, connect machines and devices in such industries as oil and gas, utilities and manufacturing. System failures and downtime in IIoT deployments can result in high-risk situations, or even life-threatening ones. IIoT applications are also more concerned with improving efficiency and improving health or safety, versus the user-centric nature of IoT applications.
What are IIoT applications and examples?
In a real-world IIoT deployment of smart robotics, ABB, a power and robotics firm, uses connected sensors to monitor the maintenance needs of its robots to prompt repairs before parts break.
Likewise, commercial jetliner maker Airbus has launched what it calls the factory of the future, a digital manufacturing initiative to streamline operations and boost production. Airbus has integrated sensors into machines and tools on the shop floor and outfitted employees with wearable tech -- e.g., industrial smart glasses -- aimed at cutting down on errors and enhancing workplace safety.
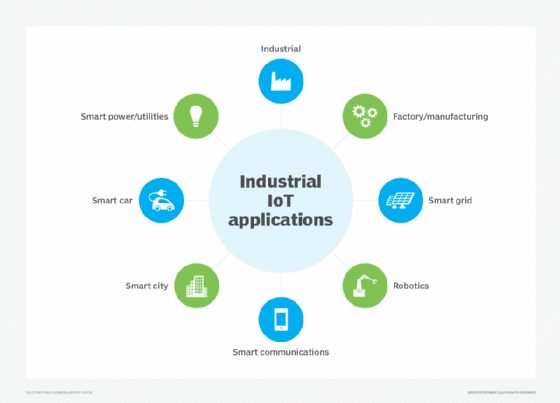
Another robotics manufacturer, Fanuc, is using sensors in its robotics, along with cloud-based data analytics, to predict the imminent failure of components in its robots. Doing so enables the plant manager to schedule maintenance at convenient times, reducing costs and averting potential downtime.
Magna Steyr, an Austrian automotive manufacturer, is taking advantage of IIoT to track its assets, including tools and vehicle parts, as well as to automatically order more stock when necessary. The company is also testing "smart packaging" that is enhanced with Bluetooth to track components in its warehouses.
Who are IIoT vendors?
There are several vendors with IIoT platforms, including:
- ABB Ability. An IIoT company specializing in connectivity, software and machine intelligence.
- Aveva Wonderware. A company that develops human-machine interface (HMI) and IoT edge platforms for OEMs (original equipment manufacturers) and end users.
- Axzon. An IIoT company focusing on smart automotive manufacturing, predictive maintenance and cold chain.
- Cisco IoT. A networking company offering platforms for network connectivity, connectivity management, data control and exchange, and edge computing.
- Fanuc Field System. A company that has developed a platform for connecting various generations, makes and models of industrial IoT equipment.
- Linx Global Manufacturing. A product development and manufacturing company offering custom IIoT, application and data management platforms.
- MindSphere by Siemens. An industrial IoT solution based around artificial intelligence (AI) and advanced analytics.
- Plataine. An IIoT company specializing in using AI to generate actionable insights in manufacturing.
- Predix by GE. A platform for connecting, optimizing and scaling digital industrial applications.
IIoT and 5G
5G is the emerging standard for mobile networks. It has been specifically designed to deliver fast data throughput speeds with low latency. 5G will support download speeds of up to 20 Gbps (gigabits per second) with sub-millisecond latency.
The emergence of 5G will likely affect the use of IIoT devices in two main ways. First, 5G's high throughput and low latency will make it possible for devices to share data in real time. Previously, this was only possible when the devices were located on private networks with high-speed connectivity. This real-time connectivity will support use cases such as driverless cars and smart cities.
The other way 5G will affect IIoT adoption is that it will likely result in device proliferation. Industrial operations might use thousands of 5G connected devices. 5G's high speed and low latency also means we'll likely see IIoT devices used in remote sites whose lack of high-speed connectivity previously made IIoT use impractical.
What is the future of IIoT?
The future of IIoT is tightly coupled with a trend known as Industry 4.0. Industry 4.0 is, essentially, the fourth Industrial Revolution.
Industry 1.0 was the first Industrial Revolution and occurred in the late 1700s as companies began to use water-powered or steam-powered machines in manufacturing. Industry 2.0 started at the beginning of the 20th century and was brought about by the introduction of electricity and assembly lines. Industry 3.0 occurred in the latter part of the 20th century and was tied to the use of computers in the manufacturing process.
Industry 4.0 is where we are today. Industry 4.0 is based on the use of connected electronic devices -- particularly, IIoT devices.
Going forward, IIoT devices will play a major role in digital transformations, especially as organizations attempt to digitize their production lines and supply chains. Additionally, big data analytics will evolve to incorporate IIoT data. This will make it possible for organizations to detect changing conditions in real time and respond accordingly.
Although IIoT devices have been around for several years, real-world adoption is still in its infancy. This is sure to change as 5G becomes increasingly prevalent and more and more organizations begin to realize what IIoT can do for them. There are a number of resources available online for organizations that want to get up to speed on IoT and IIoT.